Final Design and First Mold
- Arnav Patel
- Oct 7, 2019
- 2 min read
After going through feedback from last week, we made a few changes to our design.
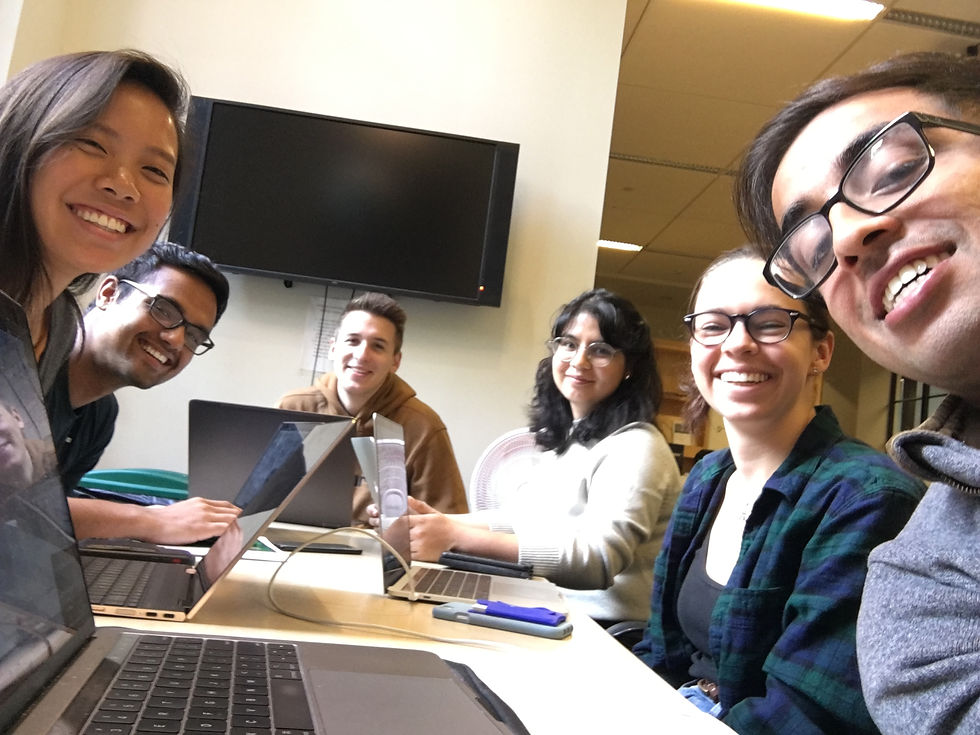
We first evaluated the manufacturing processes of each of our different components. We concluded that our landmass thermoformed die could be manufactured via 3-d printing. We created a thermoformed die to satisfy this aspect of the yo-yo design, and it can be found in the picture below.
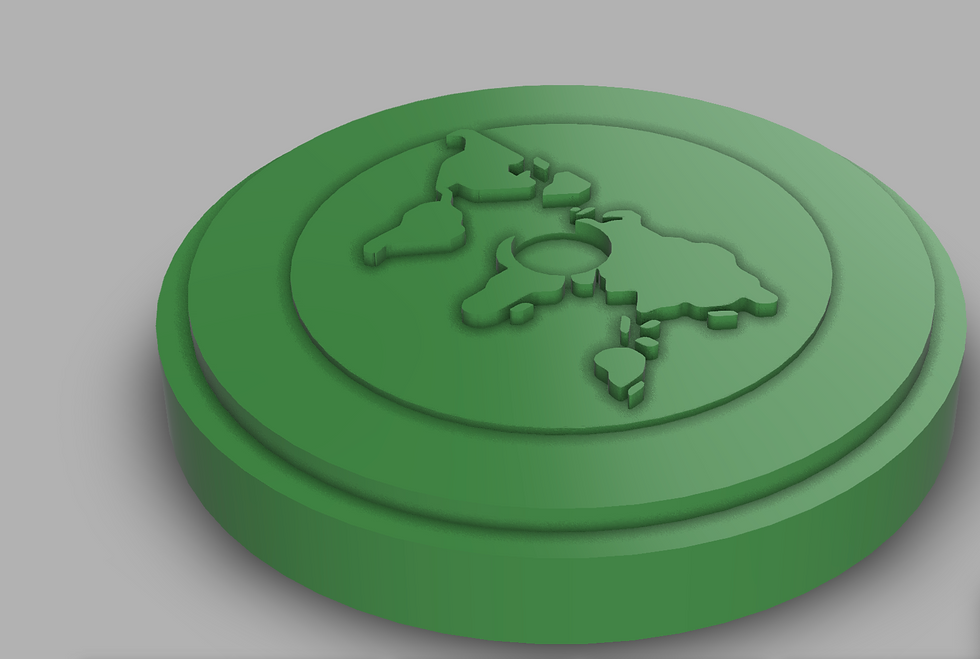
We also agreed to laser cut the water plate. Currently, we are evaluating different acrylic options for the plate. Updates to this will come later.
Additionally, we edited our wind turbine design in order to make it more balanced and symmetric across the origin of the turbine. The edits have been made to create this wind turbine.

We also edited the bearing inside the structure that holds the wind turbine. Our initial design used a toy bearing found on Amazon. We eventually realized that it cost too much and had not great tolerances, so we switched to standard larger bearings found on McMaster Carr. Our response to this was to make sure our hub was bigger for insertion.

In addition, we edited the method of insertion. Originally, the wind turbine was made to have a plastic axel. Instead, after debating the feasibility and effectiveness of such a method, we chose to have an insert molded pin to act as a shaft to fit into the hub.
Finally, we created our mold for the inside casing. This was the hardest mold to build on the grounds that it had holes and intricate structures on the inside to rest the water plate and landmass.
At the end of the day, we came to find two different molds with different methods for shut-off services. Each mold has its issues in terms of machinability. Both molds need to have fileted edges, and the sharpness of the holes in question may lead to certain problems. We are exploring solutions, and in doing so, we will be able to determine which mold we want to use.


Moving forward, the big questions we have are the following:
Can we use some of the bioplastics we have researched?
What type of pin should we use for the rotation of the wind turbine (straight dowel pin, grooved dowel pin, spring pin)?
Does the lab have any pins to test with?
Is the draft angle necessary for such a small extrusion?
What is the process to get reimbursed and order things off McMaster Carr so we can get materials quickly and not in a week?
Comments