Changes and New Molds
- Arnav Patel
- Oct 26, 2019
- 1 min read
Last Monday, we presented our final inner casing molds to our lab. We then proceeded to try to use them to create our first injection molded part. However, we ran into an issue regarding the molds' ability to close.
The extrusions on our core did not fully match the inlets in our cavity. It resulted in the flat faces of the molds not being perfectly flush with one another. This proved to be a problem we attempted to fix over the next week.
We approached the situation by altering the depths and shapes of the inlets in the cavity. If we could make these holes big enough to allow the shut-off surfaces to enter and allow for a flush interface between cavity and core, it would be ideal. We know that we may not have the best inner casing post-processing, but that is fine considering our accelerated timeline.

We also machined our wind turbine mold. This mold was interesting because of the circular runner we added in order to allow for an appropriate sized thickness and length of the wind turbine. See the picture below.
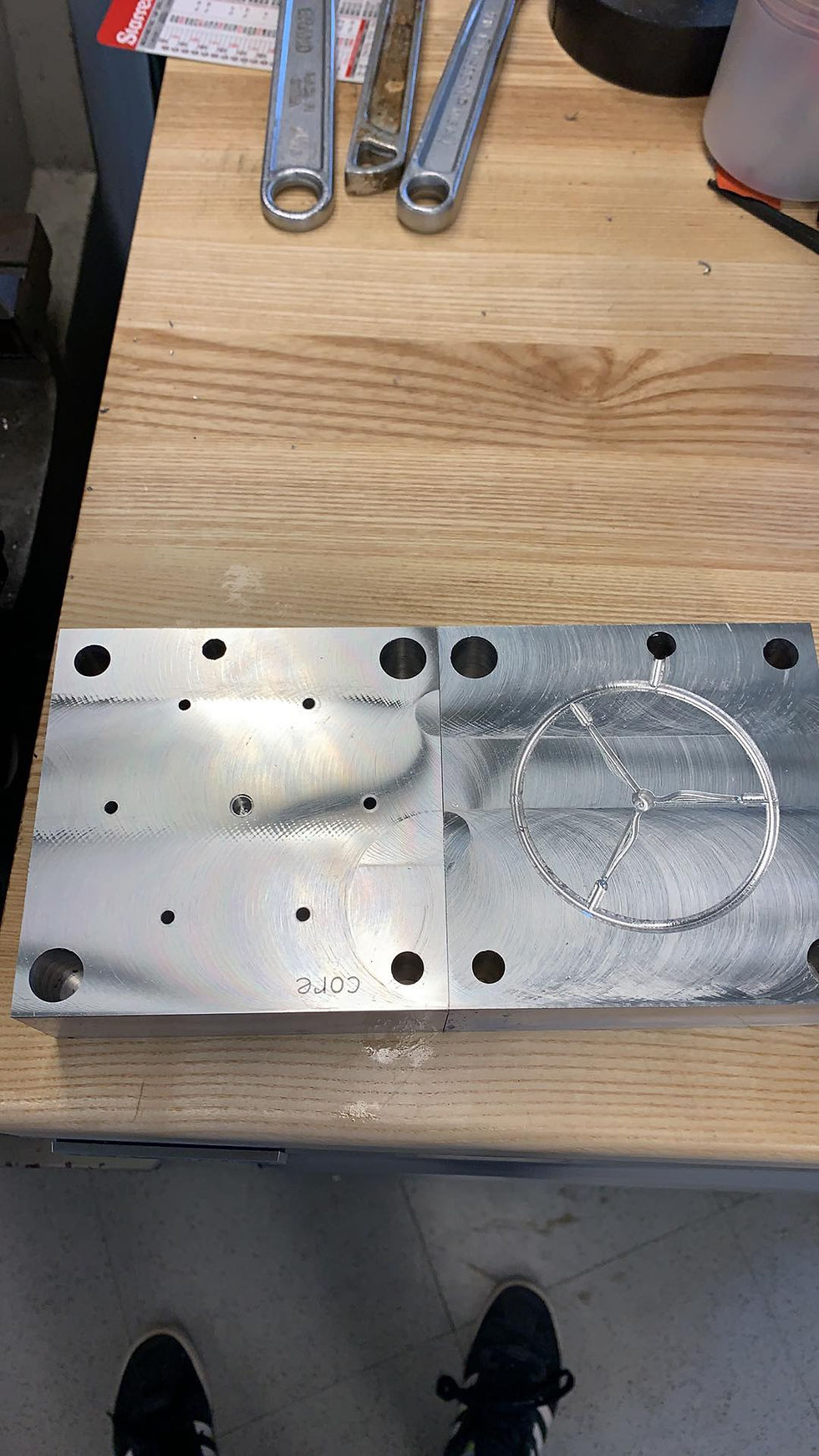
We also got the outer core CAMed and will be machining this later next week.
Finally, we 3d-printed the Earth Plate thermoforming die. We used the thermoforming machine to test out our first Earth plates. They came out well!
The next steps include modifying the inner casing mold, machining the outer casing mold, and conducting numerous tests to reflect shrinkage, fit, and other aspects of our design.
Comments